【太平洋戦争下における日米航空産業の生産・品質管理技術の懸隔に関する考察】 -大量生産ノウハウの蓄積の観点から-
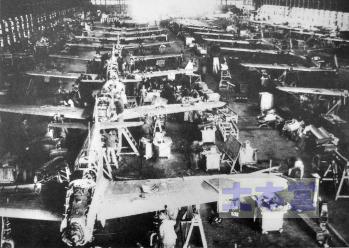
《はじめに》
太平洋戦争は、航空戦力の優劣が勝敗を決する最も重要なファクターの一つとなった戦いであり、日本も乏しい国力を挙げて優秀な航空機の開発に邁進しました。その成果の中には欧米の水準に勝るとも劣らないものが少なからず存在し、「物量でアメリカに敗れはしたが、技術力では決して負けていなかった」という言説が随所で聞かれるのも頷けます。
しかし、航空戦力の建設とは、優れた飛行機を開発すればそれで終わるものではありません。カタログ通りの性能を持つ機体を、効率よく生産出来て初めて、戦備として完整されるのです。換言すれば、設計・開発陣(トップ・エンジニア)の頭脳がいくら優秀でも、生産と品質管理を司る技師(ミドル・エンジニア)のためのノウハウが欠けていれば、全ては画餅に終わります。その意味では、設計・開発力のみならず、生産・品質管理能力も、航空産業の技術力の重要な一部分として評価しなければなりません。そして、我が国は後者の蓄積が深刻に不足していた、という認識が本投稿のモチーフです。そのような状況で日本の航空産業は如何に戦い、そして敗れたのか。少し長くなりますが、お付き合い頂けますと幸いです。
《劣悪な品質と生産効率》
予兆は早い段階からありました。開戦前に試作機が完成したにも拘わらず、戦争中期まで量産化できなかった艦爆「彗星」がそれです。画期的新機軸を幾つも投入された同艦爆は、「アウトレンジ攻撃を可能とする長大な航続距離」と「敵戦闘機をも振り切る高速性能」を併せ持つ最新鋭機として、帝國海軍の期待を一身に受けて登場しましたが、独ダイムラー・ベンツ社製DB600エンジンを国産化した「アツタ」エンジンの高度なメカニズムが災いして生産に深刻な遅延を生じ、前線での整備も困難を極めたため、最終的に性能の劣る日本製エンジンへの換装を余儀なくされました。(陸軍の戦闘機、飛燕も同じ憂き目に遭っていますね。)
また、戦争後半に満を持して登場した2,000馬力級エンジン、「誉21型」(疾風、紫電改、銀河等に搭載)は、離昇馬力で米軍の「R-3350-53」(B29に搭載)と同等、出力重量比・排気量当り馬力では30%以上凌駕するという、まさに日本の設計・開発技術の粋とも言うべき傑作でしたが、複雑な構造のため製造上の不具合が絶えず、量産品は性能低下が顕著でした。設計者の中川良一氏は、「エンジン馬力はかなり下がっていたのではないだろうか。多分、2割くらいは。」と述べています。不良品率も高く、本エンジンの前線での稼働率は平均で20%に過ぎませんでした。
もう一つ、具体例を挙げましょう。「我ニ追イツク グラマン無シ」の電文で有名な艦上偵察機「彩雲」です。高速がウリの同機ですが、試作機に比べて量産機の速力は28ノット(52㎞/h)も低下していました。内訳は、エンジンおよび排気管の粗製により10ノット、主翼の工作不良で6ノット、胴体の工作不良で4ノット等です。エンジン(誉)の出力低下も深刻で、高度6,000mでの毎分2,900回転時の出力は1,300HP程度であり、これは設計値の7割強でしかありませんでした。本機種の稼働率は昭和20年には20%を下回っていたと言います。
まさに、「戦争の進むにつれ、あらゆる部分に故障が続出し、潜在していた無理が現れ始めた。(中略)…ガタの発生、亀裂、折損、漏油等が各部に現れ、殊にエンジンに至っては致命的にも、その信頼性を全く失ってしまった。」(奥平祿郎「戦時中の航空機の整備取扱の状況について」『日本航空学術史(1910-1945)』丸善 1990年)という恐るべき状況が現実となったのです。
ここで強調しなくてはならないことがあります。それは、航空機の機体にせよ、エンジンにせよ、設計が誤っていた訳ではないということです。日本の貧弱な生産・品質管理技術では、設計通りの性能を出すに足る品質(加工精度や素材強度)を実現することが出来ませんでした。これこそが問題の所在なのです。
ここで戦後のアメリカ戦略爆撃調査団のレポートを引用しましょう。
「日本の海軍は開戦当初の80%の作戦有効率(稼働率)を維持できるとしたが、この率は漸次下がって50%となり、ある場合には20%となった。
これらの損耗は、仕上の粗雑、原料の粗悪と管理者の貧困の三者の結合によるものである。多くの場合発動機の不調によって、前線に到着したものは三機のうち一機に過ぎなかった。」(J.B.コーヘン「戦時戦後の日本経済」)
まさに、生産・品質管理技術の未熟がもたらした結末を雄弁に物語って余りあります。
参考としてご紹介しますと、状況は電気産業においても同様でした。真空管の不良品率の高さのために、唯でさえ貧弱な日本製の航空無線電話やレーダーの信頼性は著しく損なわれていましたが、東芝のある役員は戦時下の業界団体の会合で、次のように語っています。
「我々は勿論研究所から基礎的な研究結果をどしどし工場に注入してやるのですが、それを実際に適用する者が必要なのです。その技術者がなかなか得られないので困っています。工員、職工の監督と申しますか(中略)そういうふうな意味合いの技術者、これが甚だ不足しておるのであります。或る一つの真空管に注意の主力を注ぎますと、その真空管は見る見るうちに不良率が減る。ところがそれからちょっと主力をそらしますと、またその真空管から不良品が沢山出てきて良品率が非常に少なくなってしまう。(中略)この人間の不足しておることが、確かに全体としての不良率の多い原因の一つになっておるのでありまして…(後略)」(松岡正 「戦時期電気機械工業の弱電分野における技術と技術者」『技術と文明 : 日本産業技術史学会会誌』2000年)
品質と並ぶ日本の航空産業の宿痾は、劣悪な生産性でした。詳細は後述することとして、ここでは日米の航空機の生産工数を挙げるに留めます。1944年の零戦のそれは10,000人Hでした(これは、仮に100人で分業していたとすると零戦一機を生産するのに一人平均100時間の作業を要するということです。100人×100時間=10,000人H)。対して、米国のP51「マスタング」は2,700人Hに過ぎません。爆撃機についてみると、日本の「銀河」は180,000人H、米国のB24「リベレーター」は17,350人Hです。かかる生産技術の差が、圧倒的な物量の懸隔として現れたのです。日本の航空産業は数多の優れた航空機やエンジンを開発していながら、生産・品質管理技術の貧困のために、結局は「質」・「量」ともに米国に完敗したと言っても過言ではありません。
《未熟練工が生産を担っていたのは米国も同じ》
こういう話をすると、決まって「日本では熟練工が徴兵されて、女学生のおねえちゃんなど、素人が生産現場に入っていたから…」というエクスキューズが出てくるのですが、これで話を終わりにしてはいけません(笑)。日米の航空産業の従事者数を比較してみましょう。開戦直前(1941年12月)のそれは、日本が31.4万人、米国が34.7万人です。これが、両国の生産が共にピークに達する2年後(1944年)には、日本が121.0万人、米国が129.7万人へと急増しています。労働者の数で見る限り、日米両国の航空産業はほぼ同規模で、よく似た動態を示していると言えましょう。この間、機体組立部門における米国の女性労働者数は、2万人弱から、37万人に急増しています(航空工業全体に占める女性労働者の割合は、1943年末の米国が36.6%、同時期の日本が10%、1945年2月には29.7%)。未熟練工が生産を担っていたのは米国も同じなのです。「(米国における)雇用者数の著しい増加の相当部分は不熟練な婦人及び16-17歳の若年者であった」(宇野博二「アメリカにおける航空工業の発達」学習院大学『経済論集』vol10 1973年)
それにも拘らず、米国の航空産業では品質の低下は生じることはなく、生産性に至っては上昇の一途を辿りました。まず、品質面では、軍の主導でアメリカ戦時規格(AWSZ1.1~1.3)が定められ、軍需生産におけるプロセス品質管理が確立されました。これにより生産の質は改善され、米軍機の稼働率は1941年の80%から1944年には85%にまで上昇しています。一方の生産性については、1941年7月に労働者一人当たりの一日の航空機生産量は重量換算で1.42ポンドでしたが、1944年7月には2.76ポンドへとほぼ倍増しています。同じ期間、日本では0.63ポンドから0.71ポンドへと僅かな改善が見られたに過ぎず、1945年には0.42ポンドへと急落しています。当然、日米間の労働者の生産性格差は拡大の一途を辿っており、1941年には日本の労働者の一人当たり生産性は米国のそれの44%(0.63÷1.42)でしたが、44年には26%(0.71÷2.71)、45年には18%となっています。労働者の数がほぼ同じである以上、生産性の格差が、生産量の違いとなって顕れました。1944年の航空機生産数は日本の2.8万機(一応、世界4位)に対して、米国は10.1万機です。かかる生産量の圧倒的な懸隔が、稼働率の優劣と相まって、航空戦力の差、ひいては戦局の帰趨を決定づけました。
日本同様、多数の非熟練工に依存しながら、これ程の成果を上げた米国の航空産業の成功の秘鑰は一体何だったのでしょうか?次項ではそれをご紹介します。
(本項のデータは主として 佐藤達夫「戦前日本軍機の特質と戦後の自動車開発に関する一考察」『技術と文明 : 日本産業技術史学会会誌』vol17 より引用しています。)
《米国の大量生産ノウハウ》
米国をして、品質を落とさずに航空機生産量の急増を可能ならしめたものは、「大量生産体制」、または俗に「フォード主義」として知られる、生産・品質管理技術の体系です。簡単にご説明しますと、生産技術としては、①製品・部品の規格化、②専用機械の導入、③作業の標準化、④流れ作業化という四つの要素が要諦となります。
① 製品・部品の規格化とは、バリエーションを絞ることで、効率よく量産を行うことを可能にするものです。1908年からおよそ20年間も生産され続け、累計1,500万台に達したフォードT型がその象徴と言えるでしょう。
② 専用機械は、未熟練工でも確実な作業が行える半自動式の加工機械を意味します。規格化された製品・部品の量産に特化した設備で、熟練工が用いる多品種少量生産のための汎用機械の対極にあるものです。前者がアルバイトの高校生でも扱えるファストフード店の調理設備(電子レンジやフライヤー)だとしたら、後者は高級寿司屋の腕の良い板前が用いる道具(包丁とまな板など)に当たります。
③ 作業の標準化は、労働者一人一人の作業を綿密な時間研究に基づいて最適設計し、未熟練工でも対応できるよう明確に定義(マニュアル化)することです。専用機械を用いるため、これを操作する作業は比較的単純です。それらを幾つか組み合わせて一人分の標準作業を構成します。
④ 流れ作業化とは、アッセンブリーライン(自動コンベアライン)の導入と同義です。③の作業標準化の段階で、各労働者の作業時間を平準化しておき、これをタクト・タイムとしてラインを稼働させます。(チャップリンが映画「モダン・タイムス」で揶揄した生産方式です(笑))
また、品質管理技術は今日SQCとして知られるもので、統計学を駆使して品質検査を行い、異常が発生した場合には原因を割り出し、これを排除するものです。
「フォード主義」は、その名の通りフォード社の生産・品質管理技術者によって完成され、1913年にハイランドパーク工場に設置された生産ラインに結実しました。これにより、それまで職人の熟練に頼っていた時代は自動車1台あたり748分かかっていた生産時間が、93分にまで短縮されたのです。言うまでもなく、「フォード主義」の本質は、移民国家アメリカにおいて、賃金の安い未熟練工を活用して(当時としては)最先端のハイテク製品であった自動車を安価かつ高品質に量産することにあります。従って、未熟練工を動員して兵器の生産を行う場合でも非常に有効に機能するのです。
しかし、戦前の米国の航空産業は、このような大量生産方法の導入には至っていませんでした。「1940年段階における航空機生産の特徴はハンド・メイド的性質にあった。熟練工は部品を汎用工作機械によって少量製造し、(中略)機体組立においては多種多様な機種が同一フロアーで並行して製造されていた。」「だが、参戦後には量産化が至上命題となり、機種の削減と航空機部品の標準化がすすめられ、生産はアッセンブリーライン方式に変更され、44年までにはほとんどの工場に導入された。」「この大量生産方式の導入は一方では生産性を大幅に上昇させるとともに、他方では未熟練労働者に短期間で機体製造技術を習得させ、(中略)熟練工に替わって、婦人労働者を中心とする未熟練工の雇用を拡大する技術的基盤を提供した。」「自動車生産方法として全面開花した大量生産方法が、戦時要請に応じて航空機生産に大規模に適用され、航空機生産の飛躍的拡張を決定づけた」(堀一郎「第2次大戦期におけるアメリカ戦時体制の実態について」『経済学研究』vol30 北海道大学)
このように、巨大な自動車産業の存在があって初めて、航空産業における大量生産が確立されたのです。米国は、自動車産業から得た生産・品質管理技術の豊富なノウハウと、多数のエンジニアのプールを有するに至っていました(1930年代後半の米国の年間自動車生産台数は300~400万台、日本は3~4万台。1940年の米国のエンジニアは大学卒だけで30万人、日本は高等工業学校卒を含めて6万人。)。戦争が始まると、デトロイトの技術と人材は一斉に軍需産業に振り向けられ、莫大な生産増加をもたらしたのです。
GM社のW.S.クヌードセン社長が兵器生産を監督する「生産管理局」の局長に就任し、民間人でありながら陸軍中将の地位を与えられたのは、偶然ではありません。また、フォード社のウィローラン工場は流れ作業ラインをもつ世界最大の工場で、24時間のフル稼働を行い、1時間につき1機という驚異的なスピードでB24を生産し、航空機工場の一つのモデルとなりました。ルーズベルト大統領がデトロイトを「民主主義の兵器工場」と呼んだのには、このような背景があったのです。
《日本の航空機増産政策の破綻》
日本の航空産業も、元来「フォード主義」とは対照的な生産方式を採っていました。すなわち、熟練労働者が汎用設備を用いて様々な製品を少しづつ作っていたのです。
しかし、このような職人芸に頼った手工業的生産では、総力戦に伴う大規模な増産には到底対応できないことは明白でした。日本政府もこの点は認識しており、1938年の国家総動員法施行以来、企画院や商工省、内務省などの中央省庁が航空機生産能力増強のための法令を急速に整備していきました。とは言え、高級官僚には「フォード主義」についての体系的知識や包括的理解が欠けていたため、究極的には「産業報国」という言葉に端的に集約される観念論や、中身の乏しい掛け声の域を大きく超え出るものではありませんでした。人とカネを集めることは出来ましたが、肝心の中身が無かったのです。
国家レベルでの大量生産体制への移行の兆しが生じるのは、開戦後に産業界が自ら旗振り役を買って出るのを待たねばなりません。とりわけ大きな役割を果たしたのは、日本経済連盟会(経団連の前身)が1942年に設置した「産業能率増進委員会」です。
同委員会は、各企業から生産・品質管理の実践経験豊かな人材を多数抜擢しており、実際的な調査・研究が精力的に進められました。その集大成とも言えるのが、政府に提出された「機械工業に於ける多量生産実現具体策」です。この中には、製品・部品の規格統一、専用機械の導入、作業の標準化、流れ作業の導入など米国式大量生産技術(フォード主義)のエッセンスが遺漏なく盛り込まれていたのみならず、括目すべきことには、生産・品質管理技術を担う技師(ミドル・エンジニア)の大量養成機関を設置することが謳われていました。
委員会はこの後、航空産業を中心とする主要な軍需産業へ生産・品質管理技術を伝播する活動に注力し、戦後の経済発展へも少なくない影響を与えました。(本項の詳細は 佐々木聡 「太平洋戦争期における「科学的管理」の一側面」『経営と情報』静岡県立大学経営情報学部 1992年 をご参照下さい)
しかし、上記の「機械工業に於ける多量生産実現具体策」が纏められたのは1943年3月であり、この時点で既に日本の頽勢は明らかとなっていました。戦局の挽回を焦る軍部は、ほどなく過大な生産要求をねじ込むようになり、航空産業が合理的に実現しうる生産量との間の整合性は全く失われました。軍部の無謀な要求を満たすために日本政府(軍需省)が採った施策は、民需産業の大幅縮小と学徒勤労動員により大量の人員を捻出し、人海戦術で増産を図るというものでした。これは、産業界が志向した技術による生産性の向上とは本質的に相容れないことは言うまでもありません。ここに、国家レベルでの秩序だった大量生産技術導入運動は、事実上頓挫するに至ったのです(昭和19年度の生産要求は海軍25,380機、陸軍27,120機の合計52,500機。これに対し、実際の生産機数は前年度比69%増の28,180機)。
以上の経緯から、日本の航空産業における大量生産技術の導入は、戦時下のほぼ全期間を通じ、各企業の生産・品質管理技術者(ミドル・エンジニア)たちが、草の根的に苦心を重ねて進めていくことを余儀なくされていました。
《我が航空産業の敢闘》
逆境の中にあっても、日本の技師たちは航空機量産の為にベストを尽くしました。このことは、かつての敵に他ならぬアメリカ軍の戦略爆撃調査団が認めています。「米国の航空機生産高と比較すれば、日本の生産は大きくなかったが、両国の相対的な資源-材料、人的資源および技術開発―を考慮すれば、日本の努力は称賛に値する」(『現代史資料39・太平洋戦争5』)
彼らの労苦は並大抵のものではありませんでした。何故なら、課せられた使命が、単なる生産性の向上などではなく、生産メカニズムそのものの根本的な転換だったからです。
「一連の変化を、「技能から技術への転換」と捉えてもよいだろう。いかに優れた現場技能があろうとも、ある部品はこちらの神様、ある特殊加工はまた別の神様と、部品ごと工程ごとに特定の熟練技術者の力を頼まねばモノが作れない状況に、工場の限界が示されていた。最終的には、誰がやっても同じ結果が期待できる最適の工作法と工程を確立することが目標になるのである。」「モノづくりの実権が現場技能者から技術者に移っていくわけだ」「日本の機械工業全般で考えるならば、「生産技術」そのものが課題となったのは、おそらく史上初めてのことだった。生産技術とはすなわち量産技術であり、当時の具体的な目標としては、専用工作機械を多用した流れ作業方式となるのだが、それをいかに実施するかということが大問題であった。」
(「「後発国」日本における生産技術形成-航空エンジンの量産に至る道」 前田裕子 1999年)
既にご紹介した生産性と品質に関するデータが示す通り、日本の航空産業における技師達の試みは不完全なものに終わりました。しかしそれは、戦後の経済発展へと繋がる一大画期であったことも確かなのです。以下、大量生産技術の個別要素ごとに、成果と限界とを見ていきましょう。
① 製品・部品の規格化
結果からいうと、これは完全に失敗しました。軍部の場当たり的な新機種開発と用兵思想の混乱に加えて、陸海軍の対立という偏狭なセクショナリズムが多種多様な航空機とエンジンの同時生産という最悪の結果をもたらしたのです(一例として、独ダイムラー社製DB600エンジンは、陸海軍が個別に生産ライセンスを取得し、海軍は「アツタ」、陸軍は「ハ40」として生産していましたが、工場も別々なら、部品の互換性もありませんでした)。米国戦略爆撃調査団は、「(日本の)海軍は53の基本形式と112の変種を考え出し、陸軍は37の基本形式と52の変種を、即ち、合計90種の型式と164の変種を作り出したのである」と驚きをもって記しています(J.B.コーヘン 前掲書)。他ならぬ日本の軍部が、総力戦の本質を理解していなかったという事実を示す、端的な事例と言えるでしょう。
② 専用機械
専用機械についても、軍部はその必要性を全く認識していませんでした。「自動機ないしは高能率高性能の特殊(専用)工作機械を使用して兵器を作るという方法は(中略)国家的意識にはのぼっていなかった。」「当時の日本では自動機による消耗兵器の生産はむしろ異端視された。軍の指導部は機銃弾や砲弾は国民の忠誠心によって多くの人手で製造されるべきであり、機械によって自動的に作られたのでは国民の精神動員に役立たないと考えた」(『日本の工作機械工業発達の過程』日本工作機械工業会、機械工業振興協会 1962年)
実際、世界水準に達する航空機を続々と開発できるようになった日中戦争期に至っても、日本は工作機械を完全には自給できず、高度な機械については外国、しかもアメリカからの輸入に頼っていました。1937年に4,100万円だった工作機械輸入額は、急増する軍需のため、2年後の1939年には1億5,200万円にまで膨張しています(この年の工作機械の輸入依存度は金額ベースで37.3%に達しました)。
当時の産業調査レポートからは、悲痛な叫びが聞こえてきます。
「我国工作機械工業の製造する工作機械の大部分が、所謂汎用工作機械であり、特殊(専用)工作機械製造は極めて貧弱である。しかもここで特殊工作機械と言うのは周知の如く高速旋盤、精密ネジ切旋盤、治具ボール盤、歯切機械等であるが、是等の特殊工作機械が今日の機械工作上、最も重要である所から注意しなければならぬ。而して、この種特殊工作機械に就いては、(中略)なお大部分を国外より供給を仰がねばならない状態にある。」(豊崎稔『日本経済と機械工業』科学主義工業社 1940年)
このように、日本の航空産業は、ほぼゼロスタートで専用機械の製造に着手するしかなかったのです。三菱重工の場合、工作機械の設計・生産を担ったのは名古屋発動機製作所(以下、名発)に所属する「工作技術部」でした。この部署には優秀なエンジニアが集中的に配置され、専用の工場まで持っていました。「1939年9月に着工した新設の専用工場は、建物面積5,000坪、工作機械800台という大規模なものである。ここで治工具や専用工作機械が次々と製作され、専門の工作機械メーカーを驚かせた」(前田裕子 前掲)
このような努力の末に、三菱重工では1944年に稼働した名発第三工場において工作機械の国産化が実現され、設置された2,000台の機械の3分の1が専用機械でした。「1938年設立の第一工場の工作機械は輸入汎用機が主流であったから、その後数年の間に専用機械を多用するシステムへと変化したことが見てとれる」(前田裕子 前掲)
中島飛行機でも、「1935年には、工程工具班(現在の生産技術部に相当)を発足させ、米国ダグラス社出張で見た治具や水圧機による量産方式を参考に、大量生産の基礎となる新鋭機械の製作・導入…など生産性向上につながるあらゆる研究を行った」(「スバル車の歴史」)。
かくして、日本最大級の中島飛行機武蔵野製作所では、1938年にはアメリカ製輸入工作機械の割合は50%でしたが、1944年には23%にまで低下したのです。
また、ユニークな事例としては、日産自動車が1933年に招聘した米国人技術者W.R.ゴーハム氏が挙げられます。同氏は日米開戦後に日本国籍を取得、「合波武克人」と名乗り、日産傘下の機械メーカー「国産精機」で航空エンジン用の専用工作機械の設計に辣腕を振るい、母国と戦いました。
こうした取り組みの結果、国産の工作機械製造額は、1937年の5,000万円(重量にして3.2万t)から、国産化率100%が達成された(というより輸入が途絶した)1944年には7億2,300万円(12.9万t)にまで拡大したのです。しかし、多くの場合、国産工作機の性能は劣悪でした。「国産工作機の摺動面の摩耗は米国機械の摩耗の数十年分に匹敵した。精度は1、2か月で急速に低下した。カタログにある最大回転数を出すと機械は振動し、軸受は加熱した。同番数の舶来機が十分耐える重切削に於いて、国産機は振動し換歯車は折損したり曲がったりした。油圧ポンプや電気部品は故障が続出した。材質の不良、加工の不正確、これに起因する耐久力及び精度の不足が歴然としていた。」「米国製ドリルが楽々と穿つ穴を和製のドリルは数倍の時間を喰らい、次から次へと折損していくというような例が多かった」(奥村正二「技術史を見る眼」『技術と人間』 1975年)
また、依然として「工作機械に万能式が多いため生産能力が低く、取扱いに熟練を必要とした」(佐藤達夫 前掲)という指摘もあります。このため、熟練工の徴兵と未熟練工の大量投入に伴い、品質と生産効率の両面で問題を生じたのです。
結論として、工作機械の専用化は一定の成果を収めたものの、その程度は米国に比べて遥かに低い水準に留まり、性能も十分なものではありませんでした。このため、大量生産体制構築の試みが挫折する一因となりました。
「太平洋戦争下の日本の航空機および兵器の生産を設備工作機械の面から概括するとき、それは技術的に古い生産方式に依拠していたということができるのである。欧米では軍需生産の遂行に当たり…高能率の自動機ないしは特殊(専用)工作機械を使用し、生産現場にたずさわる人数をできるだけ減少させようとしたのであるが、日本は…工程細分化方式に固執し、いたずらに設備工作機械台数を増加せしめ、労働力を浪費したのである。」(『日本の工作機械工業発達の過程』日本工作機械工業会、機械工業振興協会 1962年)
③ 作業の標準化
作業の標準化のためには、前近代的な労使関係にメスを入れるところから始めなければいけませんでした。従来の日本の航空産業の製造現場は、「個人請負の熟練工が幅をきかせ、個人の出来高請負給により高額の報酬を得ていた。しかしこのシステムでは、出来高単価の高い部品の過剰生産と出来高単価の低い部品の不足という問題を生じ、完成品の製造が阻害されていた」(佐々木聡「第二次大戦期の日本における生産システム合理化の試み -中島飛行機武蔵野製作所の事例を中心に-」『経営史学』Vol27 1992年)というありさまだったのです。
このため、中島飛行機では、まず直接的な労務管理体系を確立し、それにより初めて作業の標準化を進めることができるようになりました。同社の武蔵野製作所では、戦争中期の組織改編で設置された「企画部」(技術管理部門)のもとにおかれた「作業企画課」が中心となって、作業の標準化を進めていきました。「(作業企画課は)作業標準時間・作業余裕率の制定、標準作業基準の調査、作業工程・作業動作の分析などの業務を担当した。作業企画課による作業研究を基礎に、同じ企画部の作業整備係が実際の作業工程を管理した。たとえば機械加工作業では、「作業指示書」を発行して、作業の順序、方法、程度を具体的に示した。(中略) こうした作業統制の過程を通じて、手仕上げ作業の廃止・機械化という作業の省力化が漸次進められていった。たとえば研摩作業や仕上げ作業では5%、歯車作業では20%の作業の節約が実現し、塗装作業では実に98%の省力化が実現されている」(佐々木聡 前掲)
一方、三菱重工でも、名古屋発動機製作所に所属する「工作技術部」(1940年に設置)が主体となって作業の標準化が進められていきました。「「作業指令の図面化」と「時間研究」が統合されておびただしい数の作業票が作られた。作業票には細分化された指定作業、工具、工法、作業時間等が記入され、誰でも間違いなく効率的に機械加工作業ができることを狙った」(前田裕子 前掲)
このように、作業標準化は確かな進展を見ましたが、専用機械の能力と普及が十分でなかったため、熟練工の暗黙知を完全に排除するには至らず、工員の練度低下に伴う生産現場の劣化を防げませんでした。それでも航空メーカー各社は敗戦の日に至るまで必死の努力を続けたのです。これには、次のような背景があるものと思われます。
「戦時期の産業統制政策では、一般に限られた経営資源の「量」をいかに配分するかという点に重きがおかれていたといえる。これに対し、政策の対象となる経営主体では、経営資源のなかでもとくに人的資源の「質」の向上の可能性を重視して、生産効率の維持・向上に努めた。経営諸資源が欠乏してゆくなかにあってこそ、残る唯一の生産性向上の可能性を人的資源にもとめたのである」(佐々木聡 前掲)
④ 流れ作業化
日本の航空産業における流れ作業の導入は、比較的早い段階から始められていました。機体製造では、日米開戦直前の1941年9月、三菱重工の名古屋航空機製作所が道徳工場に設置した陸軍百式司偵の生産ラインが、その嚆矢です。中島飛行機も1942年に流れ作業を導入し、航空機生産がピークに達した1944年には両社の主力工場の殆どに普及していました。その成果は大きく、米国戦略爆撃調査団は「1942年に本格的な組立ライン方式を採用して以来、1944年までに、その生産を以前の能力の8倍以上に拡大している」と評価しています。
しかし、その内実は米国とは較ぶるべくもありませんでした。戦略爆撃調査団は一方で、日本の機体製造方式を「未熟な生産ライン技術」とも表現しています。
その理由の一つは、流れ作業化の対象の不徹底にあります。流れ作業が導入されたのは、最終組み立て工程に限定されていました。製造工程全体の所要工数における最終組み立ての割合は僅か8%に過ぎず、部品の加工組立(65%)等、ほとんどの作業は旧態依然たる方式に依存していたのです。
もう一つの理由は、内容の不徹底です。最終組み立てにおいてどうにか実現された「流れ作業」は、機械力(ベルトコンベアー)を用いた米国には到底及ばず、トロッコの上に据え付けた機体を、人力によって次工程へ手押しするという有様でした。
このような「未熟」な段階にとどまったのは、しかし、一概に航空メーカーのみの責任とは言えません。流れ作業ラインの設置には莫大な固定コストが必要となるため、一定数量の生産機数を確保できないと、却って不効率となります。そして、既に述べたように、日本の陸海軍は徒に機種を増やし、1機種当たりの生産数を減らしていました。
中島飛行機の内部資料によれば、小型機の場合「月産100機」が流れ作業導入の分岐点になるとされます。ここから類推すると、月産200機~300機程度で概ね最適な効率が実現できるものと思われます(それ以上生産数を増やしても効率は大きくは上がらない)。これに対して実際の生産数はいかばかりだったのでしょうか。航空機生産がピークに達した1944年の月産データをみて見ましょう。最多の生産機種であった零戦の場合ですら、主力工場の三菱名古屋工場で113機、中島小泉工場で206機に留まります。生産数が二番目の「隼」は中島太田工場で158機、「大東亜決戦機」として急増が図られた「疾風」は中島太田工場で217機となります。ここから、最適生産水準は勿論、分岐点を超えていたラインすら極めて限られていたことが分かります。或る研究者は、二大メーカーたる三菱・中村ですら、1944年に生産していた18機種中、分岐点を超えていたのは5ないし6機種に過ぎないとしています。(山本潔「戦時航空機生産についての一考察 -”半流れ作業”方式について-」『社会科学研究』Vol44 1992年)
エンジン製造についても状況は同様であり、1944年に三菱重工が生産した機種は、量産品に限っても9つ存在していましたが、分岐点となる「月産300台」を超えていたのは3機種(「金星」、「瑞星」、「火星」)のみ、中島は量産5機種中2機種のみ(「栄」、「誉」)というありさまでした。(佐藤達夫「戦時期中島飛行機の航空エンジン事業」『立教經濟學研究』vol67 2013年)
このため、三菱・中島とも主力工場にはベルトコンベアーによる機械式流れ作業を導入できたものの、前者(名古屋発動機製作所)は最終組立工程、後者(武蔵野製作所)はピストン製造工程に限られました。(笠井雅直 「戦時下における航空機産業の研究開発と生産システム」 『名古屋学院大学論集 社会学編』vol37 2001年)
このように、一機種当たりの生産数の少なさが、日本の航空産業における流れ作業導入のネックとなっていたのです。
⑤ 品質管理
品質管理における日米の格差については、もはや多言を要しません。そもそも加工精度のレベルからして、桁違いだったのです。エンジン部品の場合、米国の許容誤差は1ミクロン単位、対する日本は10ミクロン単位で、戦争後半期には更に劣化していきます。これに、品質検査のためのノウハウと検査員の深刻な不足が加わりました。
結果は、当然ながら際立って高い不良品率として顕れます。エンジンの場合、米国ライト社が平均10%前後であったのに対し、三菱名古屋発動機製作所は45~49%(前田裕子 前掲)に達しました。機体製造では、三菱で38.4%、中島で55%です。(佐藤達夫 前掲)
これでは、工場を動かす時間と資源の半分が、不良品を生み出すために費やされていると言っても過言ではないでしょう。
戦後の話になりますが、次のようなエピソードが伝わっています。GHQがあまりにも頻繁に電話が不通になるのを訝しみ、日本軍の残党による妨害工作を疑って徹底的に調査したところ、結果は電話機の製造不良にあることが分かり、「日本人はSQC(統計的品質管理)も知らずに戦争を始めたのか」と呆れたというのです。これが、当時の日本の品質管理の水準でした。
《結び》
1945年8月、日本は戦争に敗れました。このことは同時に、航空産業における生産技術者たちの必死の努力が潰えたことを意味しました。彼らの挑戦は、米国の水準には遥かに及ばずに終わったのです。戦後、GHQは日本の航空産業の解体を命じ、ここに日本人自身の手による航空機の開発・製造の歴史は、ひとたび終止符をうたれることになりました。
「もし零戦の後継機がもっと早く完成していたら…」これは戦史に興味のある人間なら誰しも考えることでしょう。或いは、戦後米軍に鹵獲された疾風や紫電改が、ベストなコンディションのもとでの性能試験では、ヘルキャットやマスタングに勝るとも劣らない性能を示したと聞き、溜飲の下がる思いをした方も少なくないはずです。しかし、これまでの考察から、私は、戦中の日本の貧弱な生産技術力では、零戦や隼程度の航空機を「中量」作るのが限界であったと考えます。航空戦力に関する限り、長期にわたる総力戦での勝算など、初めから無かったのです。
それでは、生産技術者たちの苦闘は、全く水泡に帰したのでしょうか?答えはノーです。戦中の航空機生産から得られたノウハウと人材の真価は、戦後の民需産業、とりわけ自動車や電機産業で遺憾なく発揮されました。戦時下の日本の航空産業が、大量生産体制の要素を取り入れつつも、汎用機械と熟練工を組み合わせた手工業的側面を排除できなかったことは既に述べたとおりですが、このような生産様式の混合こそが、戦後日本の製造業の優位性を決定づけた「リーン生産」の原点となったのです。
20世紀末、日米の自動車産業の競争力の懸隔を調査したMITの調査チームは次のように記しています。「大量生産では未熟練あるいは半熟練の労働者が、一つの目的にしか使えない高価な機械で製品を仕上げる。このメカニズムは、標準化された製品を大量に生み出す。この結果、製品は安くなっても、消費者が多様な製品から好きなものを選ぶことはできない」「これに対して、リーン生産は手作りと大量生産の利点を兼ね備え、両者の欠点(手作りのコスト高、大量生産の融通性の欠如)を克服しようとするものだ。そこで組織のあらゆるレベルで多様な能力を持つ労働者のチームを編成し、応用力(汎用性)のある自動化された機械を使い、バラエティに富んだ製品を適量作ることを目指す」「北米や欧州の自動車産業はいまだにヘンリー・フォードの時代とほとんど変わらない大量生産システムに依存しており、新たな生産方法を開拓した日本企業にはとても太刀打ちできない-これが我々の結論だった」(J.P.ウォマック他「リーン生産方式が、世界の自動車産業をこう変える」1991年)
かくして日本は、大量生産体制の不徹底のため太平洋戦争に敗れ、同じ理由により戦後の経済競争で米国に一矢報いたのです。日本経済の復興と今日の繁栄は、戦時中に基礎づけられた生産メカニズムの発展的継承があって初めて可能であった-この知られざる事実を指摘して、本投稿の締めくくりとしたいと思います。
長文、失礼しました。